The Definitive Guide to Industrial Blower Systems: Maximizing Efficiency and Performance
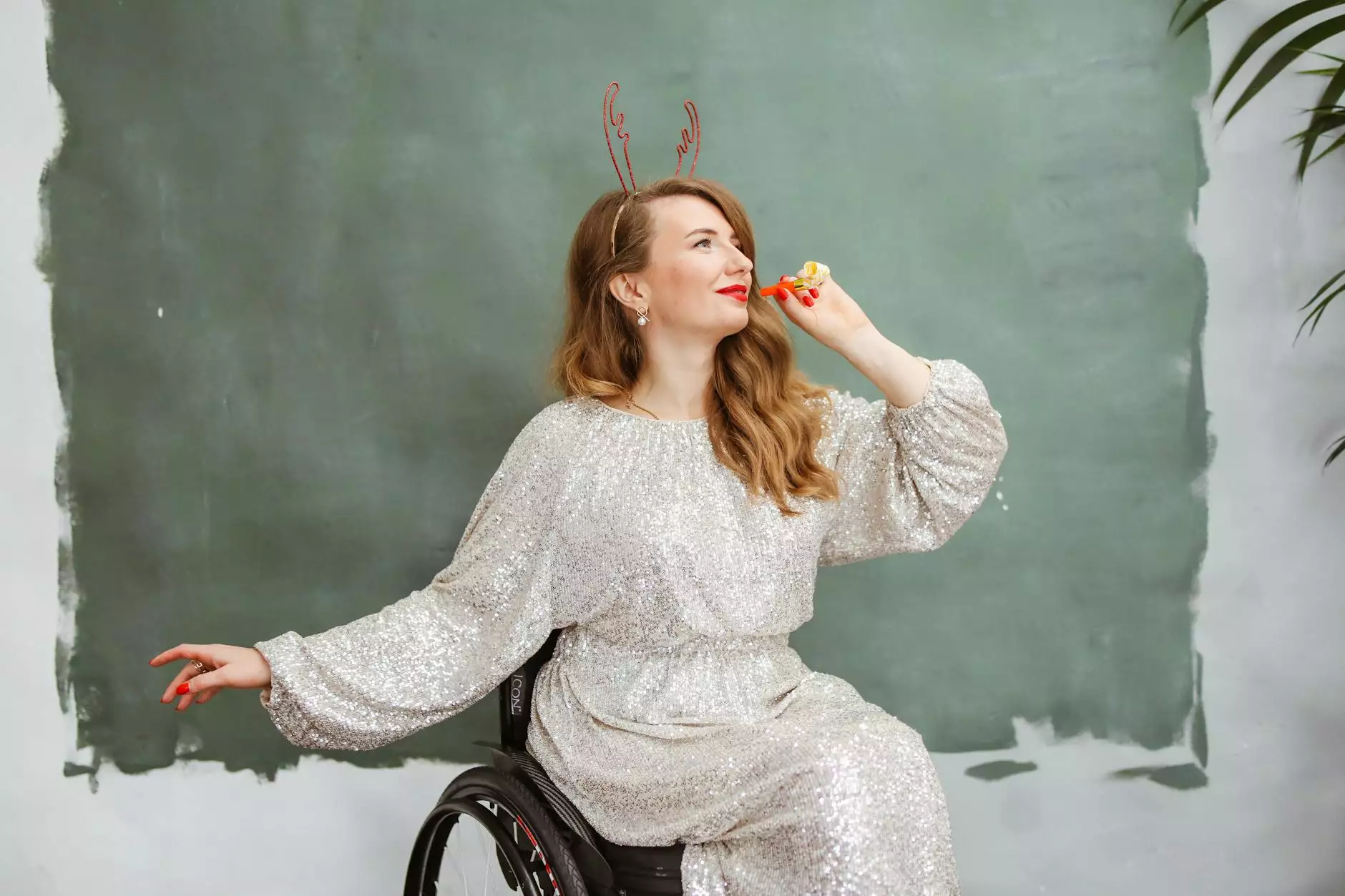
In today's fast-paced industrial landscape, effective airflow management is pivotal for operational efficiency. An industrial blower system serves as the backbone of many manufacturing operations and processes, playing an essential role in various applications. This comprehensive guide aims to unpack the many facets of industrial blower systems and their vital contributions to the success of businesses across multiple sectors.
Understanding Industrial Blower Systems
At its core, an industrial blower system is designed to move air or gas with a specific volume and pressure. These systems are crucial for delivering air or gas to the necessary points of application, thereby ensuring that operations run smoothly. Here’s a closer look at what constitutes an industrial blower system:
- Components: Typically includes a motor, blower wheel, housing, and supporting structures.
- Operation: Functions through centrifugal forces or positive displacement to create a pressure differential.
- Types: Can be categorized into different types, such as centrifugals, reciprocating, and rotary blowers.
Types of Industrial Blowers
When it comes to selecting an industrial blower system, understanding the different types available can help businesses make informed decisions. Here are some common types:
Centrifugal Blowers
Centrifugal blowers are widely used for their ability to move large volumes of air at low pressures. They are characterized by:
- High efficiency
- Utilization of rotational motion to transfer energy
- Robust design suitable for various environments
Positive Displacement Blowers
These blowers work by trapping a fixed volume of air and forcing it into the discharge pipeline. They are essential in applications requiring
- High pressure
- Constant flow rates
They are commonly used in pneumatic conveying and sewage treatment plants.
Regenerative Blowers
Regenerative blowers are designed for high flow rates with low-pressure requirements. They are often used in:
- Wastewater treatment
- Aeration applications
Applications of Industrial Blower Systems
The versatility of industrial blower systems allows them to be utilized across various industries, including:
1. Manufacturing
In manufacturing plants, blowers are used for:
- Dust collection
- Aiding in drying processes
- Cooling systems
2. Food Processing
Blowers play a fundamental role in the food industry for:
- Cooling and freezing products
- Pneumatic conveying of ingredients
3. Environmental Applications
In environmental sectors, such as wastewater treatment, blowers are essential for:
- Providing aeration
- Transporting air to biological treatment processes
4. HVAC Systems
Within heating, ventilation, and air conditioning systems, blowers provide a consistent and calibrated airflow to maintain indoor air quality.
Benefits of Implementing an Industrial Blower System
Investing in an industrial blower system offers numerous benefits that can enhance overall productivity and operational efficiency:
1. Enhanced Efficiency
Modern blowers are engineered to provide optimal airflow while minimizing energy consumption. This translates into:
- Reduced operational costs
- Longer lifespan due to lower strain on components
2. Improved Air Quality
Blowers are integral in maintaining air quality by facilitating:
- Dust and particulate removal
- Cleansing air streams in manufacturing operations
3. Versatile Applications
The adaptability of blower systems means they can be tailored to meet the unique needs of various applications, enhancing their utility in different environments.
4. Safety and Compliance
By ensuring proper ventilation and air distribution, blowers contribute to workplace safety and adherence to relevant health regulations.
Choosing the Right Industrial Blower System
When selecting an industrial blower system, it is crucial to consider several factors to ensure you choose the right system for your specific needs:
1. Application Requirements
Identify the specific requirements of your application, including:
- Required airflow rate
- Pressure capabilities
- The medium being moved (air, gas, etc.)
2. Environment Considerations
Factor in the operational environment, such as:
- Temperature range
- Potential exposure to corrosive elements
3. Maintenance Requirements
Evaluate the maintenance needs of different blower types and select one that aligns with your operational capabilities.
4. Vendor Reliability
Consider the reputation of the manufacturer and their customer support, warranty terms, and availability of spare parts to ensure reliability.
The Future of Industrial Blower Systems
The future of industrial blower systems is promising, with continued advancements in technology leading the way. As industries strive for higher efficiency and lower environmental impact, innovations such as:
- Smart technology integration
- Enhanced energy efficiency designs
- Compact and lightweight construction
will play a crucial role in shaping the next generation of blower systems.
Conclusion
In conclusion, the importance of an industrial blower system in enhancing business operational efficiency cannot be overstated. These systems not only facilitate essential processes across various industries but also provide significant benefits, including improved safety, better air quality, and increased productivity. As you evaluate your needs, it is crucial to carefully select a blower system that best fits your operational requirements and future-proofs your business against evolving industry demands. For businesses looking to optimize their processes and increase efficiency, understanding and implementing the right industrial blower system is a step towards sustainable growth.